Application of special pipes
TPEE has good oil resistance, low temperature flexibility, bending resistance, heat resistance, so that TPEE is a good material for hydraulic pipes, pipelines, and other specialty tubing, and it also has good extrusion performance. TPEE can be processed at higher extrusion speed than other materials, while the size is easy to control. Overall productivity is high.
Main application: hydraulic pipes, pipelines, spiral hose
Application
Typical applications
Hydraulic tube
Hydraulic tube is used for liquid fluids transportation. The oil is hot oil or hot phosphate ester. Tubes need high temperature resistance and low temperature flexibility. Nowadays, hydraulic pipe are using rubber, polyester fibers, nylon and etc. TPEE has many advantages that rubber doesn't have. TPEE tube has smooth inner wall: for the same fluid pressure, the wall thickness can be thinner.
Hydraulic tube advantages
TPEE hydraulic tube has high strength, elasticity, corrosion resistance, oil resistance, high temperature resistance, excellent low temperature flexibility, water resistance, UV resistance, long serve time and etc. TPEE has many advantages that chlorine rubber doesn't have: TPEE produce good tube thermal stability, excellent mechanical properties and low temperature flexibility after thermal aging.
Spiral hose advantage
TPEE has heat resistance, creep resistance, low temperature flexibility, thermal stability at high temperature, non-stick insulation layer, has low creep resistance to maintain spiral shape, excellent mechanical properties (tensile strength, elongation at break, etc.) after thermal aging, low temperature flexibility and copper stability, simplifies the production process.
The main advantage
TPEE has excellent heat resistance, the higher hardness, the better heat resistance: TPEE can be heated at 110 ~ 140 ℃ for 10h without any major weight loss, and only 0.05%, and 0.1 % at 160 ℃ and 180 ℃ respectively. So that TPEE serve temperature is very high, and the temperature can be even higher in short-term use. can be applied at automobile baking temperature (150 ~ 160 ℃), and it has little loss of mechanical properties at high and low temperatures. At 120 ℃ or higher, TPEE has much higher tensile strength than TPU, besides TPEE also has excellent low temperature performance. TPEE brittle point is lower than -70 ℃, and the lower hardness, the better low temperature resistance. Most TPEE can be applied to long-term use at -40 ℃. Because TPEE showing a balance performance at high and low temperatures, it has wide serve temperature range, ranging from -70 to 200 ℃.
TPEE has excellent oil resistance, chemical resistance to most polar liquid(such as acids, bases, amines glycol compound) at room temperature, but it cannot resist halogenated hydrocarbons (except Freon) and phenols. The resistance to chemicals increases with hardness increasing. TPEE has good anti-swelling properties and permeability resistance to most organic solvents, fuel and gas.
TPEE has wide hardness range, may vary between Shore 35D-80D, structural strength is 2-6 folds of vulcanized rubber, and has abrasion resistance, good flexibility, oil resistance and etc. Relative density is about 1.2, good mechanical strength, tensile strength greater than 30MPa, 3-6 times elastic than engineering plastics; flexural strength, and tensile strength, tear strength are 6-12 times 2-6 times 2-10 times higher than natural rubber respectively. At low temperatures, the elastic recovery is good, low temperature impact strength even better than TPU and PA11.
Physical properties
Grades | Hardness | Density | MFR(230°C/2.16 kg) | Tensile Strength | Elongation at break | Melting temperature |
---|---|---|---|---|---|---|
Test Unit | Shore D | g/cm3 | g/10min | MPa | % | °C |
H55DHT | 55 | 1.20 | 3 | 38 | 460 | 204 |
H63DHT | 63 | 1.23 | 3 | 42 | 340 | 212 |
H72DHT | 72 | 1.26 | 5 | 44 | 310 | 219 |
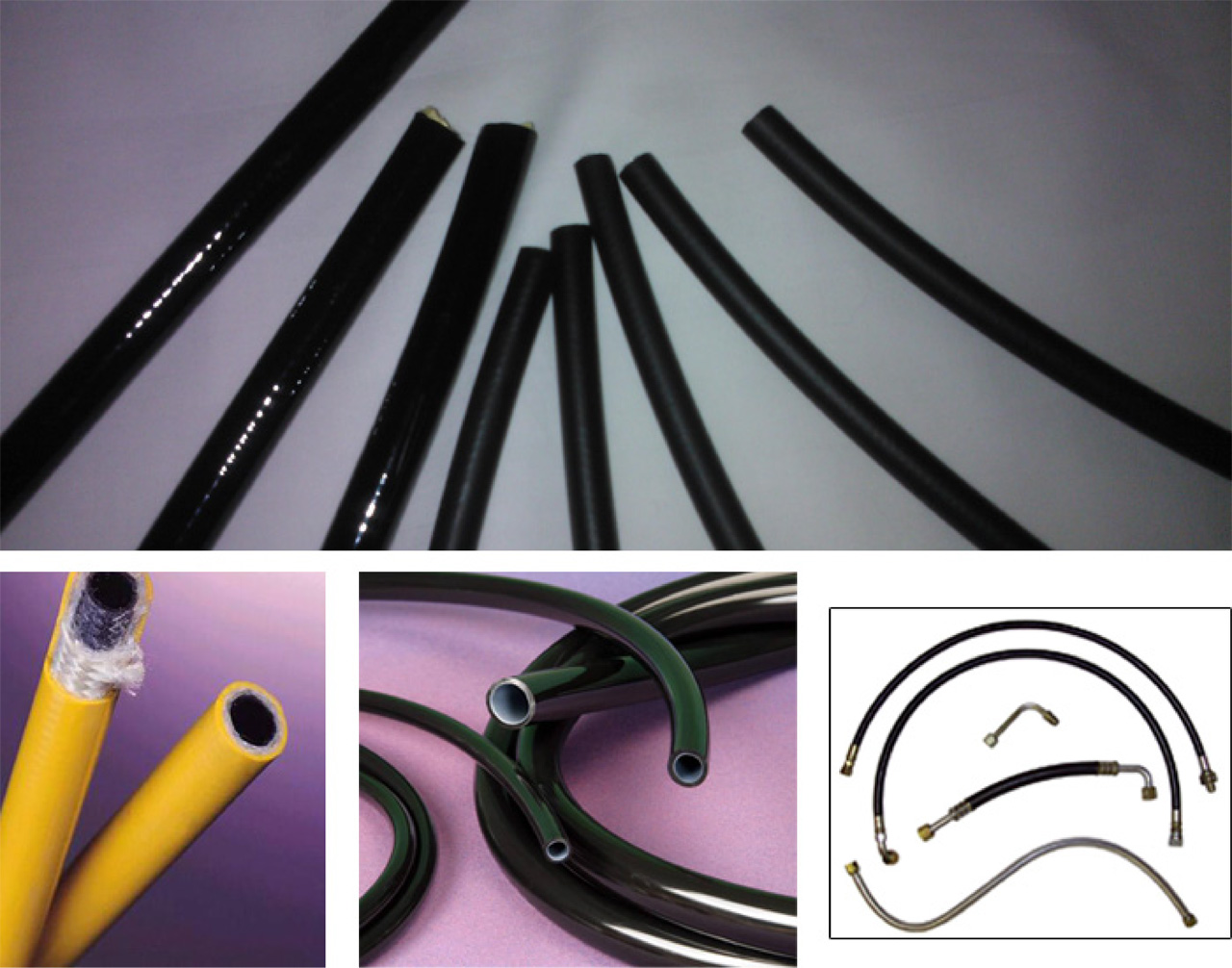